views
This article explores the transition in detail, walking through real-world scenarios, techniques, and implications of adopting this innovative cleaning solution.
A Glimpse Into the Past: Traditional Cleaning Methods
Before jumping into the functionality of a handheld laser cleaner, it helps to recall what it’s replacing. Conventional industrial cleaning involved methods like:
-
Sandblasting or Grit blasting: High-pressure abrasive media often left secondary waste and damaged sensitive parts.
-
Chemical cleaning: Harsh acids or alkalis removed contamination but posed risks to workers, parts, and the environment.
-
Manual scraping or wire brushing: Labor-intensive, time-consuming, and often inconsistent in results.
These methods, while effective in certain settings, came with operational limitations, significant waste, and health/environmental safety issues.
The Introduction of Handheld Laser Cleaner Technology
A handheld laser cleaner works on the principle of laser ablation. It uses a focused laser beam to target and vaporize contaminants from a metal or composite surface without physically contacting it. Unlike mechanical or chemical approaches, laser cleaning is a dry, non-abrasive, and residue-free process.
The appeal is simple: no abrasive media, no chemical runoff, and precise control over how and where the cleaning is performed.
But can it really stand toe-to-toe with long-established systems across industrial settings?
Let’s look closer.
Field Application: Real-World Scenarios
1. Automotive Restoration Workshops
In facilities that restore classic cars, oxidation and paint removal are daily tasks. Previously, body shops used orbital sanders and chemicals to strip rust and primer, taking hours per panel and damaging base metal layers.
A technician using a 1000W handheld laser cleaner can focus the beam to peel away rust without removing intact metal or creating airborne dust. This preserves part integrity, reduces cleanup, and shortens turnaround time.
2. Oil and Gas Pipeline Maintenance
Corrosion on external pipe surfaces is a recurring maintenance issue. Sandblasting is common but restricted in populated zones due to noise and debris.
With a laser system, maintenance teams can clean joints, weld seams, and complex profiles without containment tents or safety buffers. Laser systems have even been mounted on remote-operated arms for cleaning pipes in confined or offshore environments.
3. Aircraft Paint Removal
Removing paint from aluminum fuselage panels using traditional methods often leads to thickness inconsistencies or metal warping.
Laser cleaning, when calibrated correctly, removes paint layers without altering surface thickness. This preserves the aerodynamic profile and eliminates secondary rework, making it an emerging standard in aerospace.
The Handheld Advantage in Detail
Unlike bulky laser cleaning stations, handheld laser cleaner units allow flexible movement. Technicians can bring the system directly to the part—whether it’s a large machinery component in the field or a complex geometric surface in a workshop.
Handheld units range in power from 100W to over 2000W. Lower wattages are ideal for gentle cleaning like removing oxidation, while higher power is suited for thick paint, slag, or stubborn rust layers.
The control comes from beam modulation and pulse width, allowing the user to adjust cleaning intensity in real-time—something sandblasters or chemical cleaners can’t offer without changing media or solutions.
The Role of Surface Feedback
Modern laser cleaners often come with touchscreen control panels that allow users to set patterns, frequencies, and safety parameters. But the real evolution is the feedback loop: the visual change in the surface during cleaning acts as a direct guide. Once the laser removes contaminants, the bare metal shines through, signaling the operator to move on.
This human-visual interaction streamlines learning and minimizes over-cleaning. Unlike mechanical grinding or brushing, you’re not “guessing” how much material has been removed—you see it in real-time.
Redefining Industrial Cleaning Protocols
Facility managers in shipbuilding, power generation, and infrastructure maintenance are reevaluating SOPs to integrate laser systems. Handheld laser cleaners are being assigned to critical path tasks where reliability and repeatability are non-negotiable.
For example:
-
Power stations use them to clean turbine blades without disassembling core components.
-
Railway depots apply them to remove graffiti and prep bogies for repainting.
-
Food processing plants use lower-power units to sanitize stainless steel surfaces without introducing chemicals.
All these tasks demand precision, non-contact, and minimal disruption to surrounding operations.
Financial Factors: ROI and Lifecycle Costs
Initial investment in a handheld laser cleaner can seem steep compared to a drum of solvent or sandblasting rig. But the real math comes in operational lifecycle:
-
No recurring media costs
-
Minimal PPE or disposal expenses
-
Reduced downtime
-
Lower labor costs from faster cleaning
In three to five years, many industries report breakeven or net positive ROI. And since there’s no constant resupply chain, logistics become simpler, especially in remote or offshore operations.
The Environmental Shift
The regulatory environment is increasingly favoring green solutions. Laser cleaning doesn’t release VOCs, nor does it contaminate groundwater or generate hazardous waste. This aligns with sustainability goals across manufacturing sectors.
Switching to a handheld laser cleaner also helps companies align with ISO 14001 environmental standards, giving them an edge in international bids and audits.
Workforce Transformation
There’s another hidden factor driving this shift: skilled labor shortages. Operating a sandblaster or chemical wash station often requires training, certification, and safety monitoring. In contrast, training someone to use a laser cleaner is far quicker, safer, and often more engaging.
Younger technicians also prefer tech-driven tools. Handheld laser cleaners—with their tactile feedback, digital controls, and clean operation—are more aligned with the expectations of the modern industrial workforce.
Final Thoughts
The handheld laser cleaner is not a tool of the future; it’s a solution for today’s industrial challenges. Across sectors, it's proving to be a reliable, clean, and precise method of removing contaminants from surfaces without the pitfalls of older methods. From field service to factory floor, the adoption of this tool signals not just a technological upgrade—but a philosophical shift in how industries approach cleanliness, safety, and sustainability.
Replacing traditional cleaning isn’t about eliminating what worked—it's about refining how we do it, making it faster, cleaner, and smarter. With a handheld laser cleaner in hand, industrial professionals are now equipped to meet modern demands without compromise.
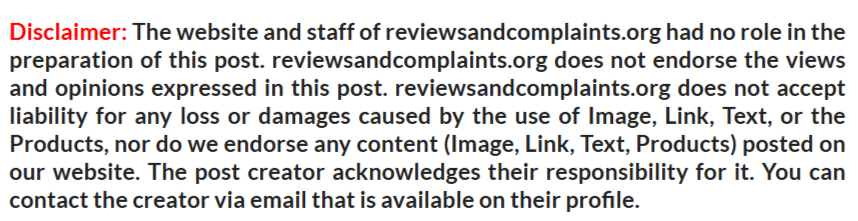
Comments
0 comment