views
Let’s peel back the layers of laser system design and explore how this scanning system became a core element of modern manufacturing.
What Is a Galvo Scanner?
The term galvo comes from "galvanometer," a device used to detect and measure electric current. In the laser industry, a galvo scanner is a motorized mirror system controlled by electromagnetic signals. When a current is applied, it moves a mirror rapidly and precisely, steering the laser beam without moving the laser head itself.
A galvo scanner system typically contains:
-
A pair of small, lightweight mirrors
-
Two galvanometers (one for the X-axis and one for the Y-axis)
-
Drive electronics
-
A control unit (usually integrated with laser software)
By adjusting the angle of the mirrors using these fast-responding motors, the galvo scanner can direct the laser beam to trace patterns, shapes, or straight lines at incredible speed—often hundreds or even thousands of millimeters per second.
Why Speed and Precision Go Hand in Hand
The misconception many have is that moving fast leads to loss of accuracy. In many mechanical systems, that’s true. But a galvo scanner breaks this rule.
Let’s take a look at what sets it apart.
No Mechanical Drag
Traditional CNC systems rely on mechanical arms and gantries to position the laser. These components carry weight, suffer from inertia, and require acceleration/deceleration ramps. In contrast, a galvo scanner uses tiny mirrors with negligible mass. They rotate, not translate. This results in ultra-fast positioning with sub-micron repeatability.
Ultra-Responsive Feedback Loops
Galvo systems operate with high-frequency feedback loops, allowing them to correct and stabilize beam position in real time. This capability is critical when working on curved surfaces or fine etching patterns that require quick directional changes.
Reduced Thermal Drift
Mechanical systems expand and contract with heat, causing slight shifts. Galvo scanners, being compact and mostly static, are far less susceptible to thermal distortion, making them ideal for long production runs with consistent results.
Real-World Use: The Invisible Engine of Laser Marking
Imagine you're producing 500 smartphones per hour, each requiring a QR code and serial number to be engraved on the housing. Doing this with a mechanical X-Y motion system could bottleneck your production line. A galvo scanner, on the other hand, can mark all items without ever moving the workpiece. It just sweeps the laser beam across the surface in milliseconds.
The laser stays fixed—only the beam moves. No positioning time. No travel lag. Only clean, crisp marks delivered at blazing speeds.
This is why galvo scanners dominate sectors such as:
-
Semiconductor traceability
-
Jewelry engraving
-
Electronics manufacturing
-
Automotive VIN marking
-
Aerospace part serialization
And even in laser cleaning, galvo scanning ensures the beam can trace complex patterns to strip paint or rust from irregular surfaces without damaging the substrate.
The Role of Software in Galvo Precision
Software control is critical. Every line, dot, curve, or engraving must be plotted and translated into exact angular movements of the mirrors. A modern galvo scanner system works hand-in-hand with CAD/CAM software that translates drawing coordinates into angular positions and motion sequences.
These systems support:
-
Variable pulse timing
-
Real-time modulation
-
Layer-by-layer patterning
-
Contour-based cleaning or marking
-
Depth-controlled engraving
So whether you're marking a flat panel or cleaning a corroded mold, the galvo scanner’s actions are tailored with surgical precision through these digital inputs.
The Galvo Scanner and F-Theta Lens Combo
To deliver the beam precisely across a plane, a f-theta lens is typically used with a galvo scanner. The scanner directs the beam at varying angles; the lens then focuses it on a flat field, correcting for beam distortion and keeping the spot consistent.
Without this combo, the laser spot would stretch and warp, reducing accuracy.
This pairing allows:
-
Uniform spot size across the entire field
-
Accurate distortion-free marking
-
Scalable field sizes depending on lens parameters
So whether you're working on a 70mm or 300mm field, the galvo + f-theta setup delivers repeatable, clean results.
How Galvo Scanners Are Calibrated
In high-precision environments, calibration is everything. Galvo scanners are calibrated to:
-
Match exact angular positions with corresponding spatial positions on the workpiece
-
Compensate for lens distortion
-
Eliminate motion overshoot or lag
Technicians use test grids, burn patterns, and feedback sensors to fine-tune the system. This means each galvo system is not just plugged in—it’s engineered for its specific role, material, and task.
Future Trends in Galvo Technology
The industry isn’t standing still. We’re seeing:
-
3-axis galvo systems that add depth control (Z-axis) for 3D engraving and large surface cleaning
-
Water-cooled galvo heads for stable operation under high power conditions
-
Fiber-coupled systems where the laser source is remote, but the galvo unit is compact and mobile
-
AI-integrated path optimization, reducing cycle time and adjusting live to part variations
These trends reflect how the galvo scanner is evolving—not just in industrial design, but also in smart automation and adaptive manufacturing.
Final Thoughts
The galvo scanner might not be the most talked-about component in laser systems, but it’s undeniably the workhorse behind high-precision, high-speed applications. It turns the raw power of a laser into a usable, targeted force—whether for engraving microchips or cleaning corroded metal parts.
Its compact design, speed, responsiveness, and integration with software make it a cornerstone of modern laser workflows. And as industries continue to demand faster, smarter, and more precise processes, the galvo scanner remains one of the most vital components quietly powering the revolution.
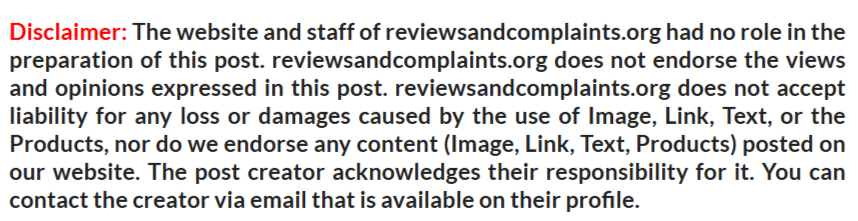
Comments
0 comment