views
Let’s dive deep into this overlooked hero and explore why it deserves more attention than it gets.
What Is a Laser Nozzle?
A laser nozzle is a precision-made component installed at the tip of the laser head. It serves as the final point from which the laser beam exits toward the material. While its appearance may be modest, its role is critical. It directs the assist gas (such as oxygen, nitrogen, or air) and focuses it around the cutting zone while ensuring the beam is accurately targeted on the workpiece.
Though small in size, the laser nozzle influences beam delivery, protects internal optical elements from contamination, and determines the efficiency of gas flow—all of which affect the cutting quality and edge smoothness.
The Role of the Laser Nozzle in Beam Delivery
Contrary to what many think, the laser nozzle doesn’t just passively sit at the end of the laser head. It actively shapes the assist gas flow, which significantly influences the interaction between the laser beam and the material surface. The nozzle size and type determine how concentrated or dispersed the gas becomes as it hits the work surface.
Too narrow, and the gas pressure may not clear the molten material effectively. Too wide, and the pressure may dissipate too quickly, leading to dross or burrs. Choosing the correct laser nozzle allows precise control of the cutting or welding environment, ensuring smoother, cleaner cuts with minimal rework.
Gas Flow and Its Relationship with the Laser Nozzle
The laser nozzle works in close coordination with the assist gas. The type of gas and the way it flows from the nozzle affect everything from material penetration to oxidation levels. For example, when cutting stainless steel with nitrogen, a fine, consistent gas flow from the right nozzle can prevent discoloration and preserve edge integrity.
A poor-quality or worn-out laser nozzle disrupts this flow, causing irregular gas distribution. This not only reduces cutting efficiency but may also damage the laser optics due to back-splatter or contamination. In this case, investing in high-quality nozzles is not an added expense—it’s a productivity measure.
Different Types of Laser Nozzles and Their Uses
Laser nozzles vary by design, material, and application. The two most common configurations are single-nozzle and double-nozzle types.
-
Single-Nozzle: Typically used for applications requiring less gas pressure, such as thin metals or plastics.
-
Double-Nozzle: Designed for high-pressure gas delivery, suitable for thick metals or deep cuts.
Additionally, laser nozzles come in various tip diameters and lengths. Each variation is tailored to a specific application or machine setup. For instance, a nozzle with a 1.0 mm tip might be perfect for delicate engraving, whereas a 2.0 mm tip is better suited for robust steel cutting.
Precision Engineering: Why Tolerances Matter
One of the lesser-known facts about laser nozzles is that they must be manufactured with extremely tight tolerances. Even a deviation of 0.01 mm in the nozzle orifice can cause the laser beam to scatter or become misaligned, leading to poor cut quality or even equipment damage.
This is why reputable manufacturers invest heavily in CNC machining and quality control. A perfectly aligned laser nozzle ensures the beam remains centered, which directly translates to improved cutting consistency and machine longevity.
Material Matters: Copper, Brass, or Ceramic?
The material used to manufacture the laser nozzle can significantly affect performance. Most nozzles are made from copper or brass due to their excellent thermal conductivity and machinability. Copper nozzles dissipate heat efficiently, making them suitable for high-power lasers.
Ceramic nozzles, on the other hand, offer excellent resistance to heat and spatter. They are ideal for applications involving prolonged exposure to intense energy or where non-conductivity is crucial. Choosing the right material depends on your specific cutting or welding needs, but in all cases, the material must endure high temperatures and maintain dimensional stability.
Why Regular Inspection and Replacement Is Necessary
Neglecting your laser nozzle is like driving a car with misaligned tires—you may not notice at first, but over time, performance suffers. Regular inspection of the nozzle orifice for wear, debris, or damage is vital. A worn-out nozzle can cause the laser beam to scatter, increase gas consumption, and degrade cut quality.
Many users make the mistake of blaming their laser machine or software when performance dips, while the real culprit is often a damaged or poorly maintained laser nozzle. Make it a habit to clean and inspect your nozzles regularly, and keep a few replacements on hand for uninterrupted productivity.
The Link Between Nozzle Alignment and Cut Quality
Nozzle alignment is another critical aspect often overlooked. Even if you have the perfect laser nozzle, poor alignment with the beam path can result in uneven gas flow or off-centered cuts. Using calibration tools and alignment pins helps ensure the nozzle is perfectly centered with the laser beam.
Proper alignment reduces thermal damage to surrounding areas and improves kerf consistency. This becomes especially important in industries like aerospace or medical manufacturing, where precision is non-negotiable.
Nozzle Size: Small Changes, Big Results
Choosing the right nozzle size is both an art and a science. While a smaller orifice might give you finer cuts, it also demands higher precision in focus and beam alignment. Larger nozzles, while more forgiving, can lead to overburn if not properly calibrated.
Matching the laser nozzle to the material type, thickness, and desired finish is essential. A minor change in nozzle diameter can mean the difference between a flawless finish and costly rework. Don’t rely on guesswork—consult your machine's documentation or supplier recommendations.
How to Choose the Right Laser Nozzle Supplier
Your laser nozzle supplier should be more than just a vendor—they should be a technical partner. Look for suppliers that:
-
Offer a wide variety of nozzle types and sizes.
-
Provide technical guidance based on your machine and materials.
-
Maintain high manufacturing standards and quality assurance.
-
Offer competitive pricing with quick delivery options.
Many reliable suppliers now offer online configurators to help you select the ideal laser nozzle based on your laser system's power, assist gas, and material type. Make use of these tools to streamline your decision-making process.
Final Thoughts
The laser nozzle may be small, but its impact on the quality and efficiency of your laser cutting system is enormous. From gas flow control to beam alignment, this unassuming part influences every aspect of the cutting or welding process. Whether you're a seasoned fabricator or just entering the world of laser technology, paying attention to your nozzles can save time, reduce waste, and elevate your final output.
In the world of precision cutting, every millimeter counts. So next time you evaluate your system's performance, don’t forget to look beyond the beam—because the secret to sharper, cleaner, faster cuts might just be your laser nozzle.
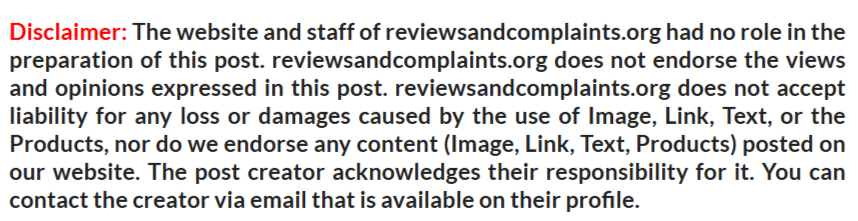
Comments
0 comment