views
Modern Innovations in Pile Driving: What’s New in 2025 for Contractors and Engineers
The construction industry has seen significant transformation over the past decade, and 2025 is proving to be another pivotal year—especially in the field of pile driving. As infrastructure demands grow and environmental regulations tighten, the pressure is on engineers and contractors to adopt smarter, safer, and more sustainable foundation installation methods.
This article explores the latest technologies, techniques, and innovations shaping the pile driving industry in 2025, offering insights for professionals seeking a competitive edge in today’s construction landscape.
The Evolution of Pile Driving: A Brief Overview
Pile driving has long been a fundamental process in deep foundation construction, used to transfer structural loads into stable soil or rock layers. Traditionally, the process relied heavily on diesel or drop hammers, manual measurements, and loud, vibration-heavy equipment.
However, as urbanization increases, land availability shrinks, and sustainability becomes a central concern, the industry has evolved. Today’s pile driving methods are more precise, data-driven, and environmentally considerate.
Key Innovations in Pile Driving for 2025
1. Smart Pile Driving Systems with Real-Time Data Feedback
One of the most groundbreaking advances is the integration of smart monitoring systems into pile driving rigs. These systems use sensors embedded in hammers, piles, and even soil to track variables like:
-
Driving resistance
-
Pile alignment and depth
-
Hammer energy per strike
-
Soil displacement
This data is transmitted in real-time to site engineers and project managers, allowing them to adjust driving force, angle, or speed instantly. The result is reduced overdriving, improved accuracy, and better quality assurance.
2. Low-Noise, Low-Vibration Equipment
As regulations increase around construction in populated or sensitive areas, manufacturers are developing pile driving equipment that minimizes noise and vibration. Hydraulic and vibratory pile drivers with frequency control are gaining popularity for their ability to reduce structural disruption.
Many machines now offer:
-
Variable frequency settings
-
Acoustic shielding
-
Shock-absorbing mounting systems
-
Remote operation to increase safety and reduce on-site exposure
These systems are essential for projects near hospitals, schools, or heritage structures.
3. Hybrid and Fully Electric Pile Driving Rigs
Sustainability is no longer optional. In 2025, an increasing number of contractors are turning to hybrid or fully electric pile driving rigs to meet emissions standards and client expectations.
Benefits include:
-
Reduced carbon footprint
-
Quieter operation
-
Lower fuel costs
-
Fewer hydraulic fluid leaks and spills
While electric rigs were once seen as underpowered, newer models now rival diesel-powered units in both force and efficiency.
4. Automated Positioning and Control Systems
GPS and laser-based positioning systems are now standard on many pile driving rigs. These automated control systems can:
-
Automatically align the pile before driving
-
Adjust the machine’s orientation to maintain vertical accuracy
-
Store location data for documentation and quality control
This automation improves both productivity and compliance, particularly in large infrastructure projects requiring millimeter precision.
5. AI-Powered Predictive Maintenance
Downtime is a contractor’s enemy. With the help of artificial intelligence, modern pile driving equipment can now predict mechanical failures before they happen. Embedded sensors track stress on joints, temperature variations, hydraulic pressure, and wear patterns, and AI algorithms analyze the data to schedule maintenance at optimal times.
This proactive approach reduces breakdowns, extends equipment lifespan, and lowers operational costs.
Software Integration and BIM Compatibility
As Building Information Modeling (BIM) becomes more central to construction planning, pile driving data is now being integrated directly into BIM systems. Specialized software tools allow engineers to simulate pile driving sequences, estimate soil behavior, and validate load-bearing assumptions digitally before work begins.
This integration offers:
-
Better collaboration between field teams and design offices
-
Clash detection with underground utilities
-
Accurate scheduling and resource allocation
By uniting physical and digital workflows, contractors can reduce rework and enhance project efficiency.
Environmental Compliance and Monitoring
In 2025, contractors are under more scrutiny than ever to comply with environmental standards. Pile driving in marine and wetland environments, for example, must meet strict thresholds for noise pollution, water turbidity, and marine life impact.
Innovative tools and practices now include:
-
Bubble curtains to dampen underwater noise
-
Bio-degradable lubricants
-
Real-time environmental monitoring dashboards
-
Non-intrusive pile extraction techniques to prevent habitat disruption
By incorporating these methods, firms not only comply with regulations but also position themselves as environmentally responsible contractors.
Case Study: Urban Bridge Retrofit Project
In a recent urban bridge retrofit project in Chicago, a contractor used fully electric hydraulic hammers equipped with real-time monitoring and automated positioning. The site was located just 50 meters from a hospital, making noise and vibration control critical.
The result:
-
40% reduction in noise levels
-
Zero structural complaints from adjacent buildings
-
25% faster pile installation time due to smart alignment features
-
Compliance with city environmental mandates without penalties
This example demonstrates how the integration of modern pile driving technologies can lead to safer, cleaner, and more profitable outcomes.
Looking Ahead: The Next Frontier in Pile Driving
Looking beyond 2025, we can expect even more innovation in the pile driving field:
-
Drone-assisted pile mapping and surveying
-
Machine-learning algorithms for soil-pile interaction prediction
-
3D-printed pile caps and supports
-
Advanced materials for lighter, stronger piles
As digital construction and automation continue to advance, pile driving will become faster, safer, and smarter.
Conclusion
For contractors and engineers, 2025 offers a host of opportunities to elevate pile driving performance while reducing environmental and safety risks. From smart rigs and electric power to AI-driven maintenance and BIM integration, the future of pile driving is here—and it’s more precise and sustainable than ever before.
To stay competitive, companies must adapt to these technologies, invest in training, and collaborate with equipment manufacturers who are leading the way in innovation.
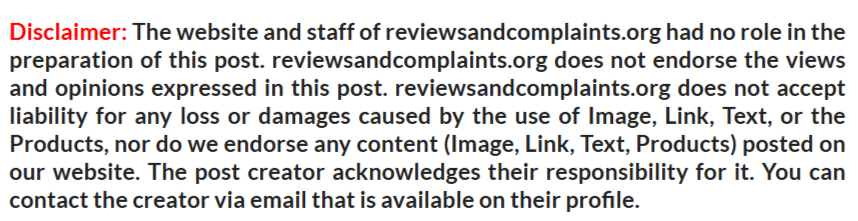
Comments
0 comment