views
In modern electronics manufacturing, achieving high-precision resistance values in compact circuit designs is not merely a technical necessity—it’s a competitive advantage. With increasingly dense PCBs and tighter tolerance requirements, manufacturers of thick film resistors rely heavily on laser resistor trimming machines to meet strict electrical specifications. This technology bridges the gap between raw fabrication and the final, fine-tuned product that performs consistently in complex circuits.
Why Trimming Matters in Modern Electronics
When resistors are first printed using thick film or thin film processes, their initial resistance values often fall outside the acceptable range. This is especially true for thick film power resistors, which are used in power supplies, automotive ECUs, industrial controls, and telecom infrastructure. Unlike standard resistors, thick film types are typically screen-printed onto ceramic substrates and fired at high temperatures to create durable, high-power components.
Despite controlled manufacturing techniques, variability in the paste, firing conditions, and substrate can lead to resistance deviations. This is where laser resistor trimming equipment becomes essential. The equipment precisely adjusts the resistance value by selectively removing conductive material in a tightly controlled manner.
How Laser Resistor Trimming Works
The working principle of a laser resistor trimming machine is deceptively simple but technologically sophisticated. The equipment uses a focused laser beam—often a solid-state or UV laser—to cut away minute portions of the resistor film. This process alters the geometry of the resistor path, increasing resistance to match the design specification.
Most systems operate under closed-loop feedback: they continuously measure the resistor value during trimming and stop the laser the moment the target resistance is achieved. The result is a resistor with incredibly tight tolerances, often down to ±0.1% or better.
There are two main types of trimming methods:
-
Abridging (or L-cut) trimming: Involves creating a notch or channel in the resistive path, effectively lengthening it.
-
Edge trimming: Reduces the width of the resistive track without changing its length.
These techniques ensure that resistors used in sensitive analog circuits, medical instruments, or aerospace systems meet exacting standards.
Applications of Thick Film Resistors in Industry
Thick film resistor applications extend far beyond consumer electronics. Due to their excellent heat dissipation, reliability, and ease of integration onto ceramic substrates, they are widely used in high-voltage or high-frequency environments. In automotive applications, thick film power resistors control ignition systems, braking electronics, and LED lighting drivers. In power supply units, they manage load balancing and voltage regulation. In telecommunications, they are part of RF filtering and antenna matching circuits.
Their popularity is also due to scalability—manufacturers can produce thousands of thick film resistor networks on a single substrate, making them ideal for large-scale electronics production. However, without accurate trimming, these resistors would introduce noise, imbalance, or signal integrity issues in precision applications.
That’s why laser resistor trimming equipment is such a crucial investment for OEMs and component suppliers. It allows them to ensure the reliability and accuracy of each resistor before integration into larger systems.
Advantages of Laser Trimming Over Mechanical Methods
Before laser trimming became standard, resistor values were adjusted using abrasive methods or by manually selecting and sorting components. These approaches were time-consuming, inconsistent, and unsuitable for mass production.
Today’s laser resistor trimming machines offer multiple advantages:
-
High precision: Real-time resistance measurement and feedback ensure ultra-precise values.
-
Non-contact process: There is no mechanical stress on the substrate or surrounding components.
-
Speed and scalability: Machines can process hundreds or thousands of resistors per hour.
-
Automation: Systems integrate seamlessly into SMT and hybrid circuit production lines.
Additionally, modern systems can handle both single resistors and resistor networks, making them versatile for manufacturers that handle diverse circuit designs.
Choosing the Right Equipment for Laser Trimming
When selecting laser resistor trimming equipment, several factors come into play:
-
Laser type and wavelength – UV lasers provide finer resolution, while IR lasers offer deeper ablation for thicker films.
-
Precision control software – Look for systems with closed-loop PID feedback for real-time adjustments.
-
Fixturing and motion control – The stability of the platform impacts cut quality and repeatability.
-
Integration capability – Compatibility with existing automation lines reduces deployment friction.
Some advanced systems also include camera-based alignment, pattern recognition, and data logging, which are crucial for traceability and quality assurance in industries like aerospace or medical electronics.
Sustainability and Yield Considerations
From a sustainability perspective, laser trimming has a low environmental footprint. It doesn’t require consumables like abrasive wheels or chemical etchants. There's also minimal waste, and no emissions or noise pollution. By improving first-pass yield rates, manufacturers also reduce scrap and rework, leading to better overall resource efficiency.
For high-value components like thick film power resistors, the ability to salvage and trim marginal parts rather than discard them can translate to significant cost savings over time.
Final Thoughts
As electronic devices become more compact, powerful, and sensitive, the importance of accurately tuned components only increases. Laser resistor trimming machines provide manufacturers with the precision, speed, and flexibility they need to meet these demands at scale. In parallel, the growth of thick film resistor applications across automotive, industrial, and medical sectors is driving innovation in trimming equipment and techniques.
For any business involved in hybrid circuit manufacturing, investing in reliable laser resistor trimming equipment isn’t just a technical decision — it’s a strategic move toward better quality control, reduced waste, and long-term competitiveness.
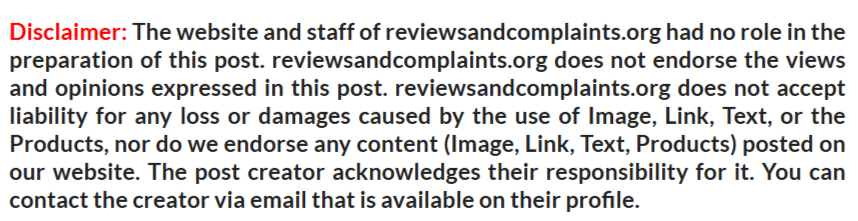
Comments
0 comment