views
In the fast-paced world of product development, the speed at which a concept moves from design to a tangible prototype is critical. One of the leading methods enabling this accelerated transformation is CNC (Computer Numerical Control) machining. Central to the effectiveness of CNC machining in rapid prototyping is the selection and use of CNC materials. These materials range from metals like aluminum and titanium to various plastics such as ABS, nylon, and polycarbonate. Each material plays a unique role depending on the functional requirements and desired characteristics of the prototype.
CNC materials influence not just the appearance of the prototype but also its performance, durability, and cost-efficiency. Engineers and designers must evaluate these materials with precision to ensure compatibility with the prototype’s intended use. A well-chosen CNC material can significantly enhance design accuracy, while a poorly selected one can lead to delays, additional costs, and structural flaws. As such, CNC materials are not merely inputs in the manufacturing process—they are strategic tools that shape the entire course of product development.
CNC Materials in the Prototyping Phase
During the prototyping phase, the choice of CNC materials is crucial in determining the speed, accuracy, and functionality of the prototype. Prototypes are often created to assess form, fit, and function, and each of these aspects can be influenced by the type of material used. Metals like aluminum are popular for their strength-to-weight ratio and excellent machinability, making them ideal for aerospace, automotive, and robotics industries. On the other hand, plastics such as POM (Delrin) are frequently used when flexibility and resistance to wear are needed in mechanical components.
The diversity of CNC materials allows engineers to replicate the intended production material characteristics without committing to expensive production tools. This flexibility speeds up the iterative design process, as prototypes can be machined and revised quickly based on real-world testing and feedback. By using CNC materials that simulate final product behavior, designers gain more accurate insights into how their product will perform under operational conditions. This reduces the risk of failure in later development stages and streamlines the path toward mass production.
Enhancing Product Design Accuracy with the Right CNC Materials
Product design is a meticulous process where every dimension, angle, and tolerance matters. CNC materials play a pivotal role in maintaining this design integrity during prototype fabrication. Unlike 3D printing, which may introduce inconsistencies in surface finish and dimensional stability, CNC machining provides high precision, especially when paired with suitable CNC materials. For instance, choosing aluminum for structural prototypes ensures a reliable and accurate rendering of the design, aiding in precise fitment and assembly evaluations.
Furthermore, the thermal and mechanical properties of CNC materials allow engineers to test their designs in realistic environmental conditions. For example, using heat-resistant materials like stainless steel or high-performance plastics enables the evaluation of a prototype's endurance under stress, temperature, and load. This insight directly informs design improvements, ensuring that the final product not only looks good on paper but also performs well in the field. Therefore, CNC materials are instrumental in refining design elements that affect usability, manufacturability, and longevity.
Balancing Cost and Performance in Material Selection
One of the critical decisions in rapid prototyping and product design is finding a balance between performance and cost. CNC materials vary widely in price, and selecting the most suitable option requires a clear understanding of both the project’s technical requirements and budgetary constraints. For early-stage conceptual models, cost-effective materials such as acrylic or ABS plastic may be chosen to quickly visualize the product. These CNC materials are inexpensive, easy to machine, and ideal for iterating shapes and aesthetics without incurring high expenses.
However, when functional testing or pre-production validation is required, more durable and high-performance CNC materials are often necessary. This is where materials like titanium, brass, or engineering plastics come into play despite their higher cost. The challenge lies in determining which material offers the best trade-off between mechanical performance and economic feasibility. By strategically selecting CNC materials based on the prototype’s stage and purpose, companies can reduce waste, accelerate development timelines, and bring superior products to market faster.
The Future of CNC Materials in Product Development
As manufacturing technologies evolve, the range and capabilities of CNC materials are expanding. Emerging materials like carbon fiber composites and bio-based plastics are becoming more accessible for CNC machining, offering new avenues for sustainable and high-performance prototyping. These advanced CNC materials not only reduce environmental impact but also provide designers with new properties to leverage, such as increased strength, lighter weight, and improved resistance to chemicals or wear.
Additionally, advancements in multi-material CNC machining are allowing for more complex prototypes that integrate different materials in a single build. This opens doors for more functional testing at the prototype stage, where parts can be produced with varying densities, hardness levels, or surface textures—all in one go. As material science continues to intersect with CNC technology, the future of product design will rely even more on intelligent material selection. Ultimately, CNC materials will not just support innovation—they will be a driving force behind it.
Conclusion
CNC materials are the unsung heroes of rapid prototyping and product design. Their properties, versatility, and compatibility with CNC machining processes directly impact how efficiently and effectively ideas are brought to life. From quick conceptual prototypes to precise functional models, selecting the right CNC materials determines the pace, quality, and success of product development. As industries continue to demand faster turnaround times and higher product standards, understanding and leveraging CNC materials will become an indispensable skill for engineers, designers, and manufacturers alike.
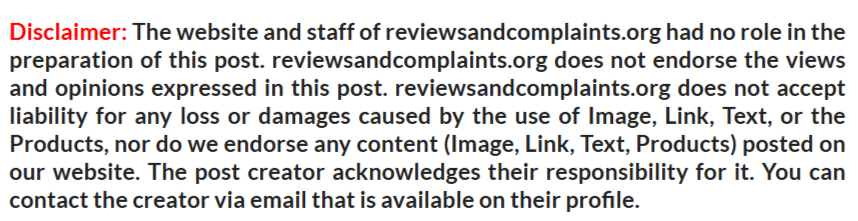
Comments
0 comment